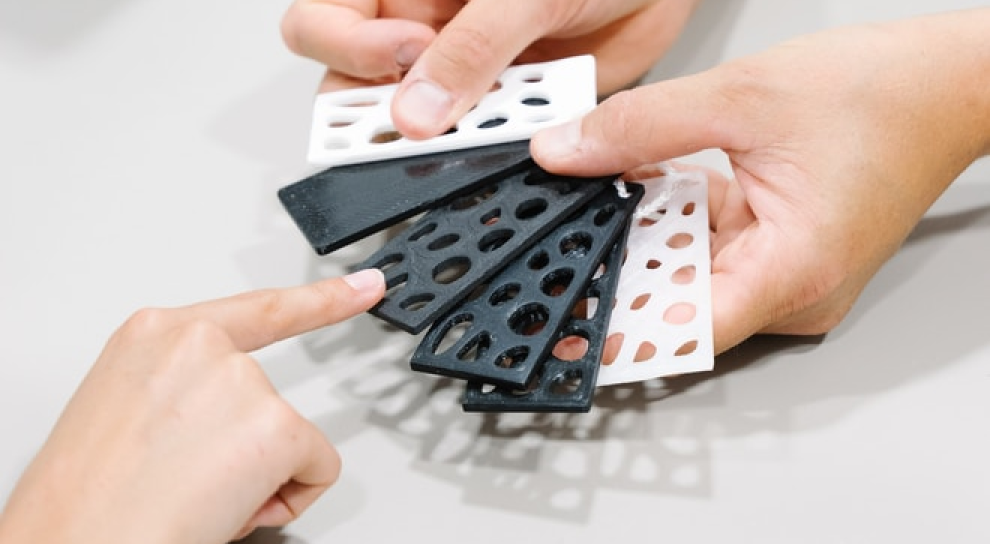
Multi Jet Fusion – MJF
Multi jet fusion 3D technology builds parts by laying down a thin layer of powder on a print bed over and over before an inkjet array in the print carriage sweeps over the print bed, jetting two agents down. One being a fusing agent and the other is a detailing agent that is used to reduce fusing near the contours of a part to achieve greater detail.
Direct Energy Deposition – DED
Directed energy deposition (DED) is a 3D printing service we offer, using the method of a focused energy source, such as an electron beam, laser or arc (PAW, GTAW, TIG) to melt material in powder or wire form which is simultaneously deposited by a nozzle. As with other additive manufacturing processes, DED systems can be used to add material to existing components, for repairs, or occasionally to build new parts.
DED allows near net shape production of relatively large parts with minimal tooling.
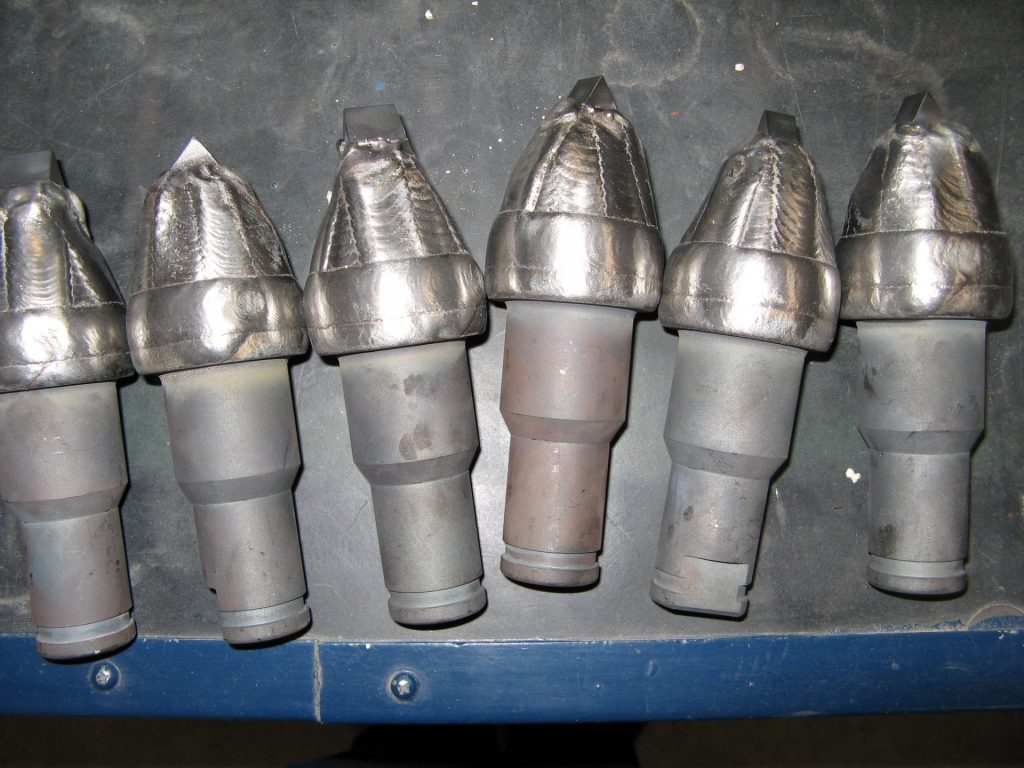
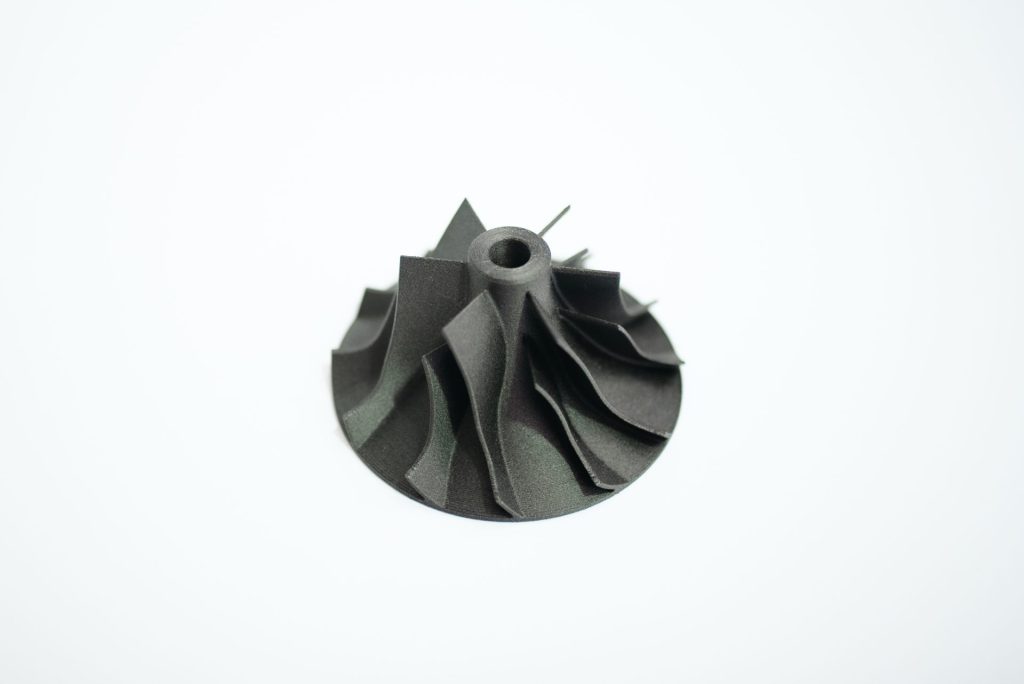
Binder Jetting
Binder jetting is an additive manufacturing process in which an industrial printhead selectively deposits a liquid binding agent onto a thin layer of powder particles — either metal, sand, ceramics, or composites — to build high-value and one-of-a-kind parts and tooling. The process is repeated layer by layer, using a map from a digital design file, until the object is complete. Binder jetting has the advantage of high speeds and material flexibility, however the process requires a furnace to remove the binding agent.
Selective Laser Sintering – SLS
Selective laser sintering (SLS) is a commonly used powder-based additive technology to create models, prototypes and end-use parts in durable, engineering-grade thermoplastics.
SLS uses a recoater to spread a thin layer of powder over the build volume. A laser sinters the cross-section of the part to fuse the powder together. The z axis then drops one layer and the process begins again until the build is complete. Parts are then excavated from the build powder-cake so the excess powder can be removed. The unused powder in the build envelope acts as the support structures which eliminates the need to remove supports after the build process. This process has considerable advantages over FDM as there is often very little redesign required. To find out more about our SLS 3D printing services, get in touch.
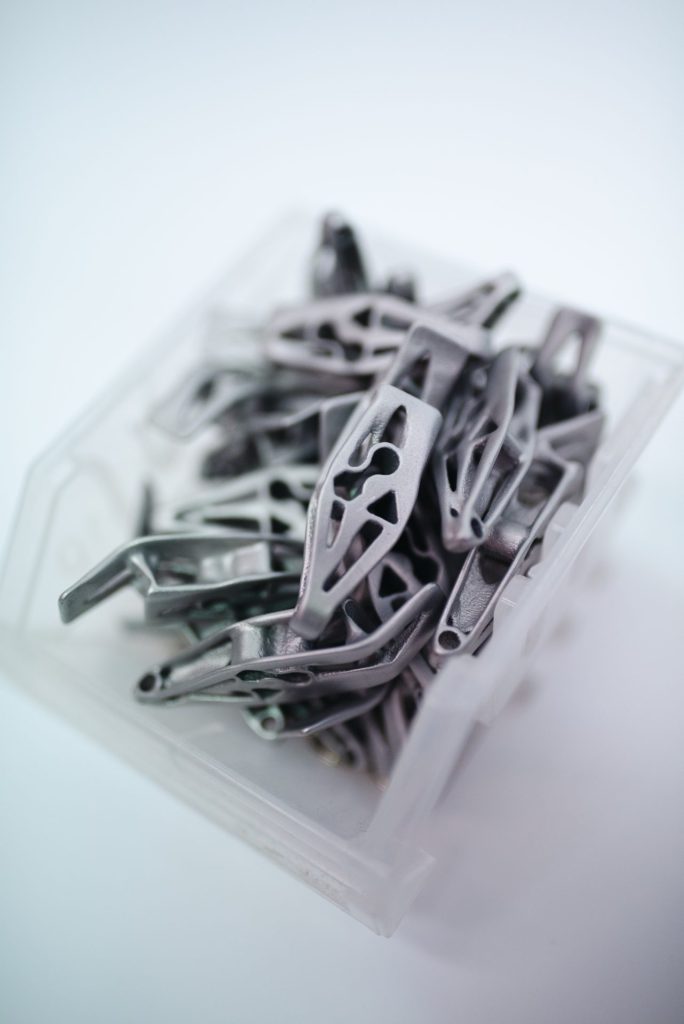
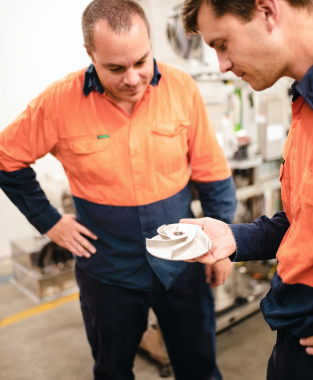
Cold Spray
Cold spray is an additive manufacturing technique that deposits powder particles in the solid state by accelerating them towards a surface within a supersonic gas flow. Cold spray can be used to coat a variety of materials (metals, glass, ceramics, polymers). This technology is mainly focused on the build of large components and is widely used for repair of worn or damaged metal components.